تحلیل بنیادی صنعت فولاد; فولادیها چقدر سود میسازند؟
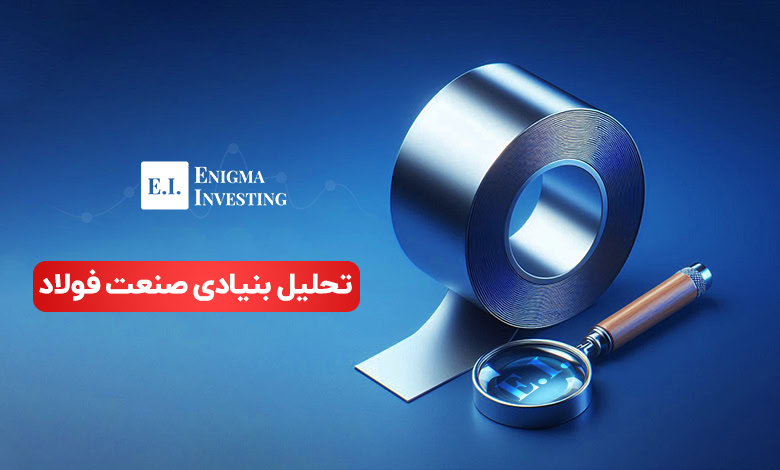
فولاد یک آلیاژ فلزی است که از آهن و کربن تشکیل شده است. با توجه به مقاومت بالا، دوام و چکشخواری این کالا به طور گسترده از آن در صنایعی همچون ساختمان، خودروسازی و مهندسی استفاده میشود. این ماده یکی از پرمصرفترین کالاها در دنیا شناخته میشود. صنعت فولاد نقش مهمی در توسعه و رشد اقتصادی یک کشور دارد. در ایران نیز این صنعت به عنوان یکی از صنایع مهم شناخته شده و نقش مهمی در رشد و توسعه کشور دارد. از این رو در این مقاله هر آنچه که باید در خصوص صنعت فولاد دانست و همچنین میزان سودآوری شرکتهای فولادی در سال 1403 تشریح شده است.
زنجیره صنعت فولاد چیست؟
پیش از آنکه به تحلیل صنعت فولاد پرداخته شود، باید گفت که زنجیره فولاد از فرآیند استخراج سنگ آهن تا تبدیل آن به محصولات فولادی، شامل مراحل متعددی است که به صورت یک زنجیره قرار دارد. هر بخش آن در بازار سرمایه دارای چندین شرکت و تولیدکننده است. ضمن آنکه تمامی فرآیند زنجیروار به هم مرتبط است. صنعت فولاد از تبدیل سنگآهن به آهن اسفنجی و سایر مواد تا آمادهسازی محصولات نهایی فولادی را شامل میشود.
بخش اول: نمای کلی از صنعت فولاد
برای تحلیل صنعت فولاد پیش از هر چیزی لازم است تا شناختی در خصوص چیستی این کالا و انواع آن، خواص و ویژگیهای فولاد، نحوه تولید و… کسب شود. در این بخش به طور مختصر به این موارد پرداخته شده است.
فولاد چیست؟
در تحلیل بنیادی صنعت فولاد باید گفت که فولاد آلیاژی از آهن و کربن است. در واقع میتوان گفت که کربن عنصر کلیدی در تولید فولاد است و فولاد را از آهن متمایز میکند. فولاد حاوی حدود 0.002 تا 2.14 درصد کربن است که این ماده فولاد را سختتر و قویتر از آهن خالص میکند. فولاد یک ماده پرکاربرد است که در صنایع مختلف از جمله اتومبیلسازی، هواپیما و کشتیسازی، ساختمان و تولید ابزارآلات و… از آن استفاده میشود. از این فلز هم به عنوان مواد اولیه و هم به عنوان ماده واسطهای استفاده میشود. با افزودن آلیاژهایی مانند کروم، نیکل، منگنز و وانادیوم، میتوان خواص فولاد را تغییر داد. بیش از 3500 گرید مختلف فولاد با خواص فیزیکی، شیمیایی و محیطی متفاوت وجود دارد.
خواص و ویژگیهای فولاد
ویژگیهای رایج فولاد در زیر ذکر شده است:
- استحکام و دوام بالا
- رسانایی
- قابلیت چکشخواری و جوشپذیری
- مقاومت در برابر خوردگی
- قابلیت بازیافت
انواع فولاد از جهت خواص و ویژگیها
فولاد خواص مکانیکی خود را بر اساس ترکیب شیمیایی یا عنصر آلیاژی تغییر میدهد. در ادامه انواع فولاد براساس خواص و ویژگیها آورده شده است:
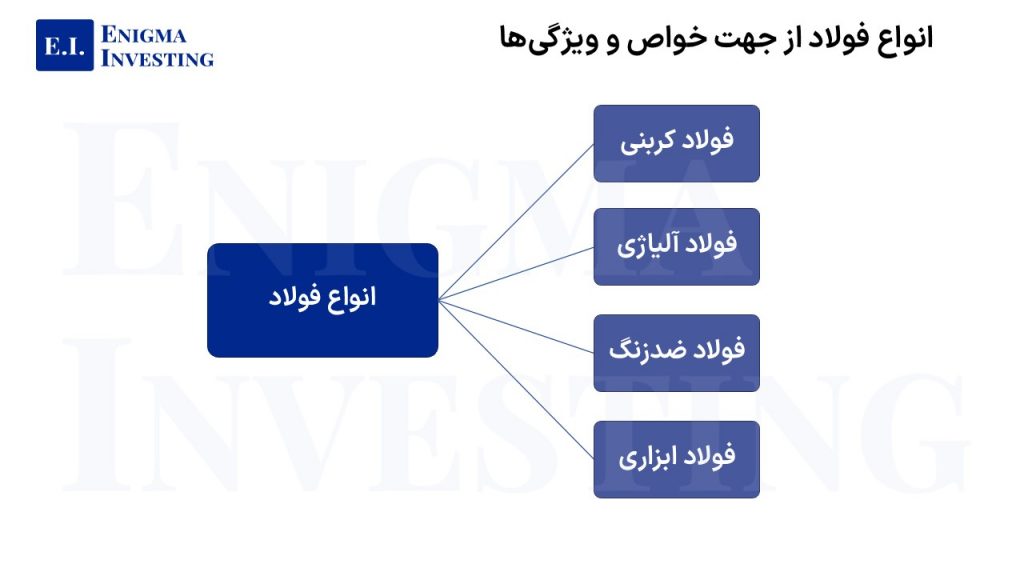
فولاد کربنی: فولاد با محتوای کربن بین 0.05 تا 2.1 درصد وزنی به عنوان فولاد کربنی شناخته میشود که بیشترین استفاده را در صنایع تولیدی دارند. بر اساس ترکیب کربن، میتوان فولاد را به چهار نوع فولاد کربنی طبقهبندی کرد:
- فولاد ملایم (فولاد کم کربن): 0.05 تا 0.30 درصد وزنی کربن- این فولاد تا حد زیادی رایجترین نوع فولاد در بازار فلزات است.
- فولاد کربن متوسط: 0.3 تا 0.5 درصد وزنی کربن- یکی از بزرگترین مزایای فولاد کربن متوسط، استحکام آن است.
- فولاد کربن بالا: 0.5 تا 1.5 درصد وزنی کربن- وقتی صحبت از سختی و چقرمگی به میان میآید، فولاد کربن بالا، گزینه انتخابی خواهد بود.
- فولاد کربن بسیار بالا: 1.5 تا 2.1 درصد وزنی کربن
فولاد آلیاژی: در صنعت فولاد، فولاد کربنی با یک یا چند عنصر آلیاژی مانند منگنز، سیلیکون، نیکل، تیتانیوم، مس، کروم و… ترکیب و فولاد آلیاژی تولید میکند. عناصر آلیاژی به دلایلی همچون بهبود سختی، استحکام، چقرمگی، عملکرد در دمای بالا، مقاومت در برابر خوردگی و مقاومت در برابر سایش و… به فولاد اضافه میشوند. به طور معمول، عناصر آلیاژی بسته به کاربرد 1 تا 50 درصد وزنی ترکیب فولاد آلیاژی را تشکیل میدهند.
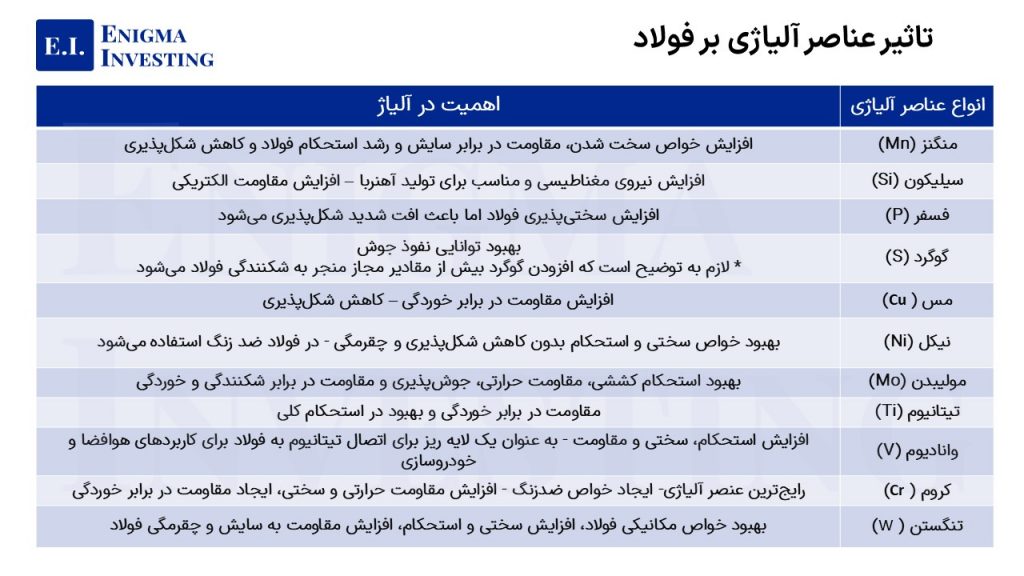
فولاد ضدزنگ: فولاد ضد زنگ یک آلیاژ فولادی حاوی 10.5 درصد کروم است. این فولاد در برابر خوردگی مقاومت بالایی دارد. این فولاد خود شامل آلیاژهای آستنیتی (Austenitic Alloys)، آلیاژهای فریتی (Ferritic Alloys) و آلیاژهای مارتنزیتی (Martensitic Alloys) میشود.
فولاد ابزار: فولادهای ابزار بین 0.5 تا 1.5 درصد وزنی کربن دارند. افزایش محتوای کربن باعث افزایش سختی و استحکام آن میشود. معمولاً از این فولادها برای ساخت ابزار و قالب استفاده میشود.
کاربردهای عمده فولاد
فولاد پراستفادهترین و بازیافتیترین ماده فلزی روی زمین است. این ماده در اشکال و آلیاژهای مختلف، کاربردهای مختلفی دارد. طبق گزارش انجمن جهانی فولاد (WSA)، عمده فولاد تولیدی (51 درصد) در صنعت فولاد، برای ساختمانها و زیرساختها مانند پلها، تونلها و… مورد استفاده قرار میگیرد.
در تصویر ذیل سهم صنایع و بخشهای مختلف در مصرف فولاد آورده شده است:
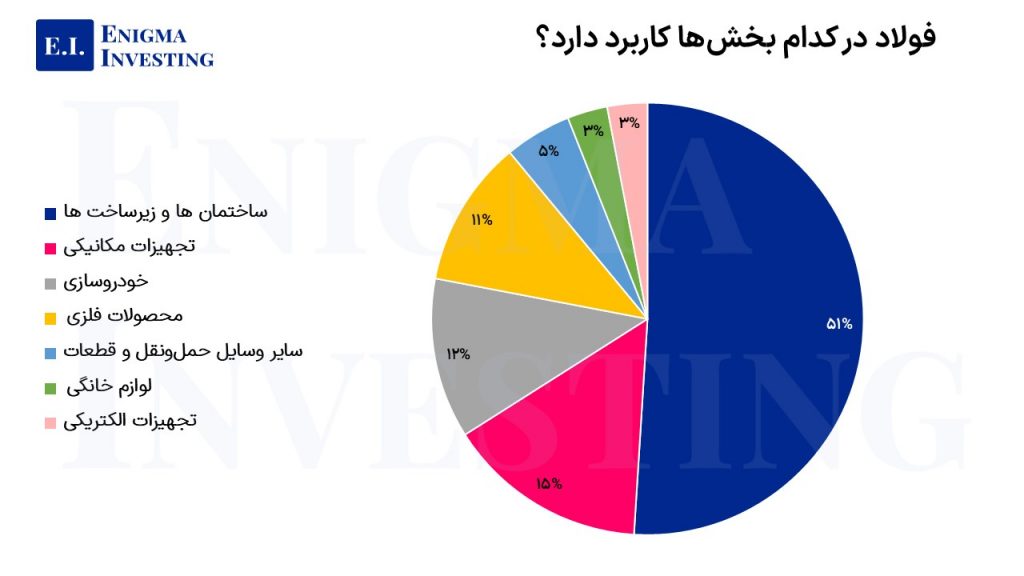
فرآیند تولید فولاد
در صنعت فولاد، فرآیند تولید بدینصورت است که از سنگ آهن کنسانتره و سپس گندله تولید میشود. از گندله آهن اسفنجی یا فولاد خام و از آهن اسفنجی محصولات میانی تولید میشود. محصولات میانی در نهایت به محصولات نهایی تبدیل میشوند. بنابراین ماده اولیه و اصلی تولید فولاد سنگ آهن است.
تصویر ذیل ضرایب تبدیل برای تولید یک تن فولاد خام را نشان میدهد:
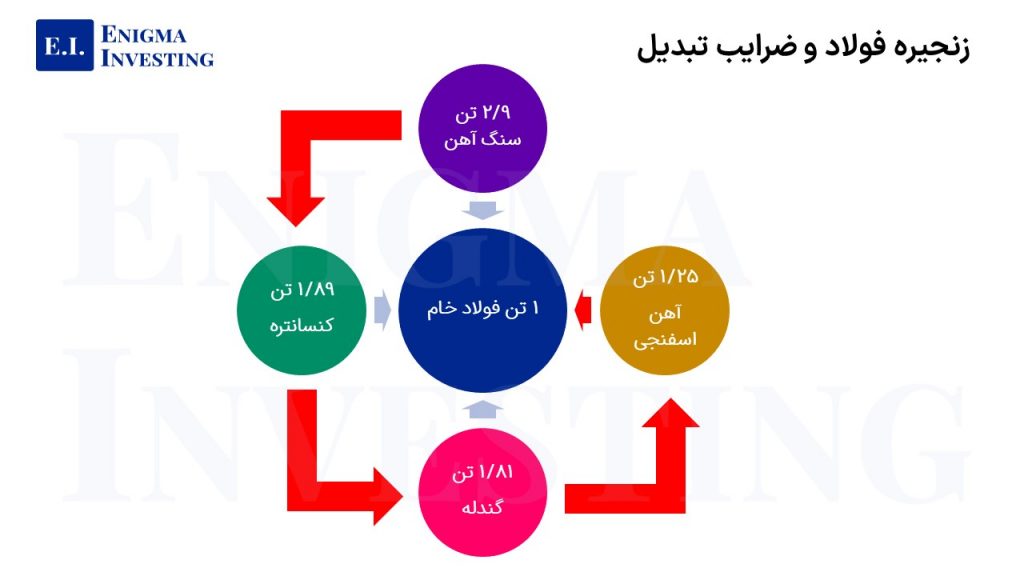
روشهای تولید فولاد
در صنعت فولاد، به طور کلی دو روش رایج برای تولید فولاد وجود دارد که شامل روش کوره بلند و روش احیای مستقیم است. بهرغم آنکه روش کوره بلند در دنیا رایجتر است، اما در کشورهایی مثل ایران که منابع غنی از گاز طبیعی دارند، بیش از ۹۵ درصد تولیدات از روش احیای مستقیم به دست میآید. در ادامه این دو روش به طور مختصر تشریح شدهاند:
1- روش کوره بلند: در این روش گندله، سنگ آهن و کک به عنوان مواد اولیه وارد کوره شده و پس از گرمایش احیا و ذوب میشوند. سپس با دمش اکسیژن و افزودن آلیاژها فولاد موردنظر تولید میشود.
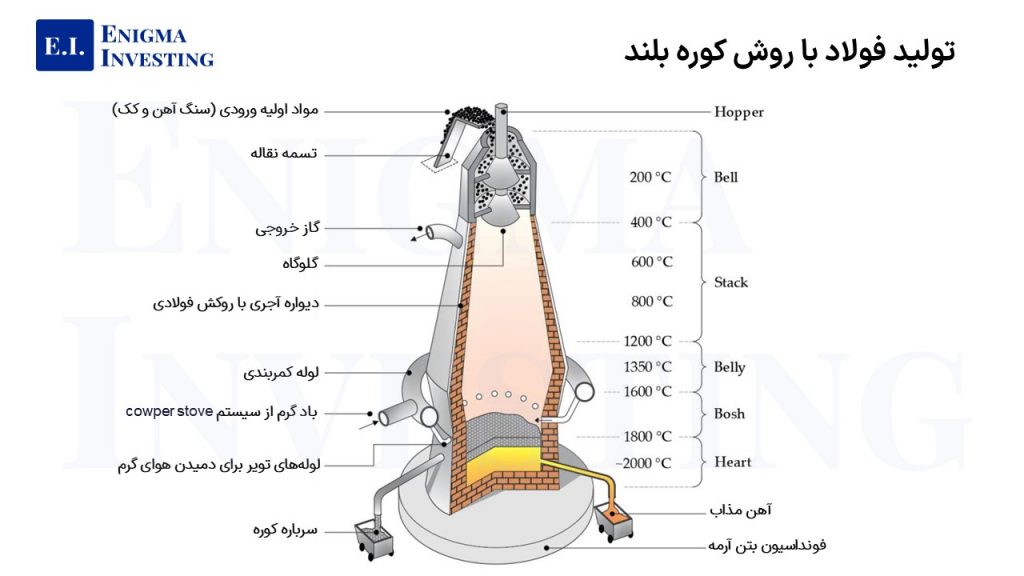
2- روش کوره قوس الکتریکی (احیای مستقیم): در این روش گندله از طریق گازهای کاهندهای همچون گاز طبیعی یا زغالسنگ احیا و به آهن اسفنجی تبدیل میشود. سپس آهن اسفنجی به همراه آهن قراضه و… در کوره قوس الکتریکی ذوب و در فرآیند ریختهگری به انواع اشکال شمش تبدیل میشود.
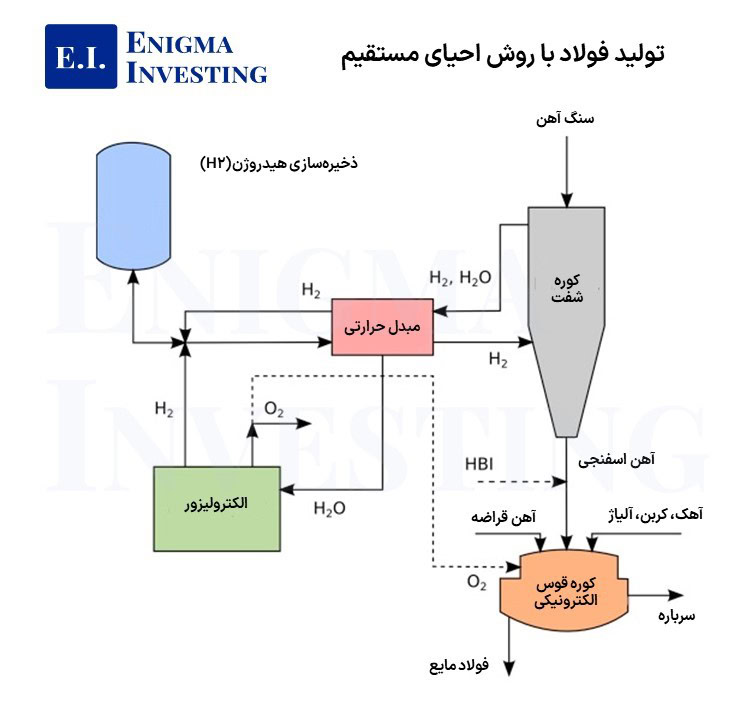
محصولات میانی و نهایی در صنعت فولاد
محصولات میانی محصولاتی هستند که پس از ذوب فولاد مذاب در کوره فولادسازی، قبل از عملآوری در قالبهایی با شکل خاص ریخته میشوند. شمش، بیلت، بلوم و اسلب محصولات میانی فولاد هستند که محصولات نهایی فولادی از آنها ساخته میشوند.
شمش (ingot): این محصول ذوزنقهای شکل و طول هر شاخه آن حداکثر ۲ متر است.
بیلت (Billet): بیلت (شمشال)، با طول بیشتر نسبت به شمش، سطحی دایره شکل یا مربعی با عرضی کمتر از ۱۵سانتیمتر (سطح مقطع کوچکتر از ۲۳۰ سانتیمتر مربع) دارد. از این محصول برای تولید میلگرد و سیم استفاده میشود.
بلوم (Bloom): بلوم (شمشه) در واقع همان بیلت ولی با اندازه متفاوت است. این محصول با عرض بیش از ۱۵ سانتیمتر (سطح مقطع بزرگ تر از ۲۳۰ سانتیمتر مربع) است. از این محصول در تولید سپری، نبشی، قوطی و ناودانی استفاده میشود.
اسلب (Slab): اسلب (تختال) برخلاف بیلت و بلوم سطح مقطعی صاف با ابعاد ۱.۲۵ در ۱۲ متر است که ضخامتی ۲۳۰ میلیمتری دارد. از این محصول برای ساخت انواع ورق فولادی استفاده میشود.
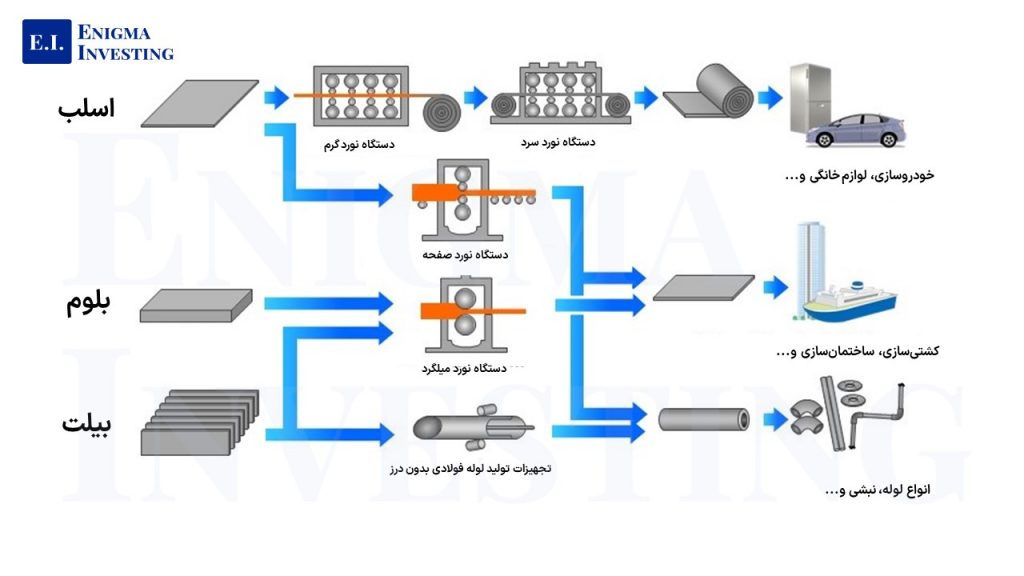
بخش دوم: تحلیل صنعت فولاد از بعد جهانی
بخش دیگری که در تحلیل بنیادی صنعت فولاد باید مورد بررسی قرار گیرد، بررسی این صنعت در سطح جهانی است که در ادامه بررسی خواهد شد.
میزان تولیدات فولاد خام در دنیا
براساس آمارهای جهانی میزان کل تولیدات جهانی فولاد خام 1892 میلیون تن بود که اختلاف چندانی با سال 2022 نداشت. این در حالی است که ظرفیت اسمی تولید فولاد خام جهانی در آن سال 2432 میلیون تن فولاد تخمین زده شده است که نشان میدهد 77 درصد از ظرفیت اسمی فولاد خام در جهان تولید شده است. از کل تولیدات فولاد خام، 71.1 درصد از روش تکامل یافته بسمر یعنی روش BOF (کوره بلند) و 28.6 درصد از فولاد جهانی به روش EAF یا کوره قوس الکتریکی (احیای مستقیم) تولید شده است.
نمودار ذیل میزان تولیدات فولاد خام جهانی از سال 1950 تا سال 2023 آورده شده است:
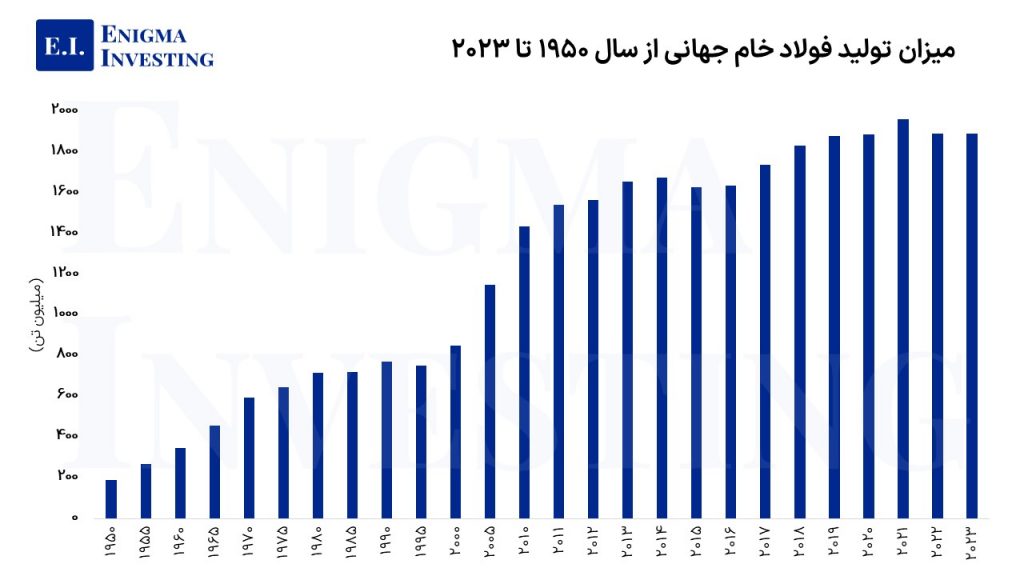
کدام کشورها بیشترین میزان فولاد خام را تولیدکردند؟
در صنعت فولاد جهانی، کشور چین سهم بزرگی (57 درصد) از کل تولیدات دنیا را دارد. این کشور در سال 2023 بیش از یک میلیون تن فولاد خام تولید کرد. پس از آن هند و ژاپن دو تولیدکننده بزرگ فولاد در دنیا شناخته میشوند. ایران به یکی عنوان دهمین تولیدکننده بزرگ فولاد دنیا در سال 2023، 31 میلیون تن فولاد خام تولید کرد که نسبت به سال 2022 رشد 1.3 درصدی داشته است. سهم این کشور از کل تولیدات جهانی 1.6 درصد است.
در سال 2023، رکود در ساختوساز واحدهای مسکونی که ناشی از نرخهای بهره و هزینههای ساختوساز بالا بوده، منجر به کاهش تقاضای فولاد در اکثر مناطق عمده دنیا شده است. در این سال افت شدید فعالیت مسکن در ایالات متحده، چین، ژاپن و اتحادیه اروپا اتفاق افتاد و انتظار میرود که ضعف در فعالیت مسکن تا سال 2024 همچنان ادامه یابد. همچنین ضعف در فعالیتهای تولیدی نیز مانع از تقاضای جهانی فولاد در سال 2023 شد.
در مقابل سرمایهگذاریهای قوی در تأسیسات تولیدی و زیرساختهای عمومی، عوامل اصلی حمایت از تقاضای فولاد در برخی از کشورهای بزرگ استفادهکننده فولاد در سال 2023 بودند و تا حدودی افت تقاضا به دنبال رکود در بخش ساختوساز را تعدیل کردند.
حدود 85 درصد از تولیدات کل فولاد خام دنیا به 10 کشور که در جدول ذیل آورده شده است، اختصاص دارد.
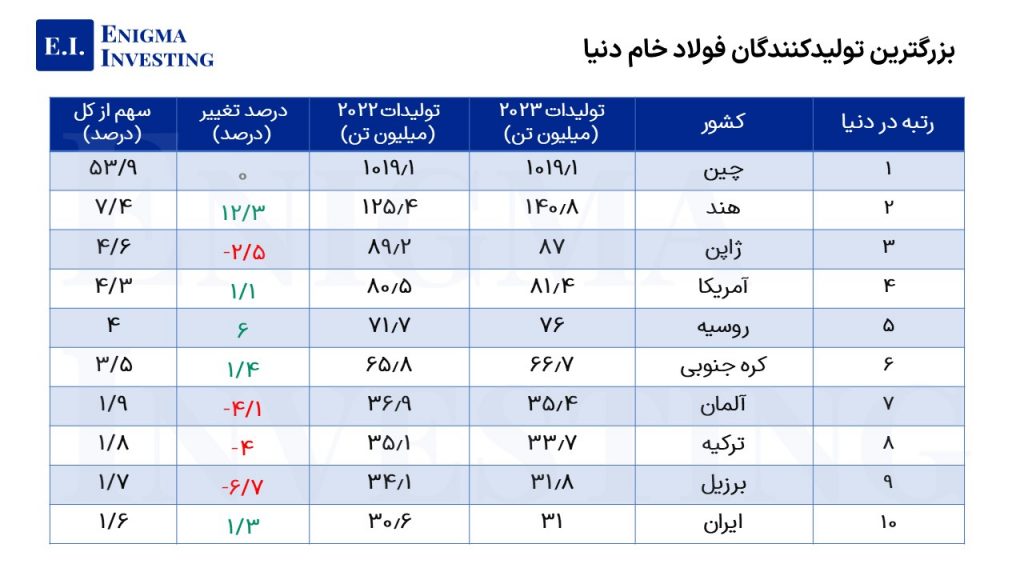
میزان تولیدات آهن اسفنجی (آهن احیاشده) در دنیا در سال 2023 برابر با 136.5 میلیون تن بود که سهم ایران از این تولیدات برابر با 33.4 میلیون تن (24 درصد از کل) محاسبه شده است.
بزرگترین مصرفکنندگان در صنعت فولاد
در سال 2023، میزان مصرف فولاد با افت 1.13 درصدی نسبت به سال 2022، 1763 میلیون تن محاسبه شد. در این سال سرانه مصرف محصولات نهایی فولاد نیز 219 کیلوگرم به ازای هر فرد بود که نسبت به سال 2022 کاهش حدود 2 درصدی داشته است. 71 درصد از تقاضای فولاد به قاره آسیا اختصاص دارد. در میان کشورها بیش از نیمی از تقاضای کل فولاد دنیا مربوط به کشور چین (51 درصد) بوده که سرانه مصرف در این کشور 628 کیلوگرم به ازای هر فرد محاسبه شده است. دومین مصرفکننده بزرگ دنیا کشور هندوستان با میزان مصرف 133.4 میلیون تن فولاد و سومین مصرفکننده ایالات متحده با مصرف 90.5 میلیون تن، بزرگترین مصرفکنندگان فولاد خام دنیا در سال 2023 بودند.
تجارت جهانی در صنعت فولاد
تجارت فولاد از فولاد خام تا آهن قراضه و محصولات فولادی را شامل میشود. حجم تجارت جهانی فولاد در سال 2023، 435 میلیون تن فولاد بود. چین بزرگترین صادرکننده دنیا است. این در حالی است که اتحادیه اروپا بیشترین واردات فولاد را به خود اختصاص داده است. پس از آن آمریکا بیشترین میزان واردات را در دنیا داشته است.
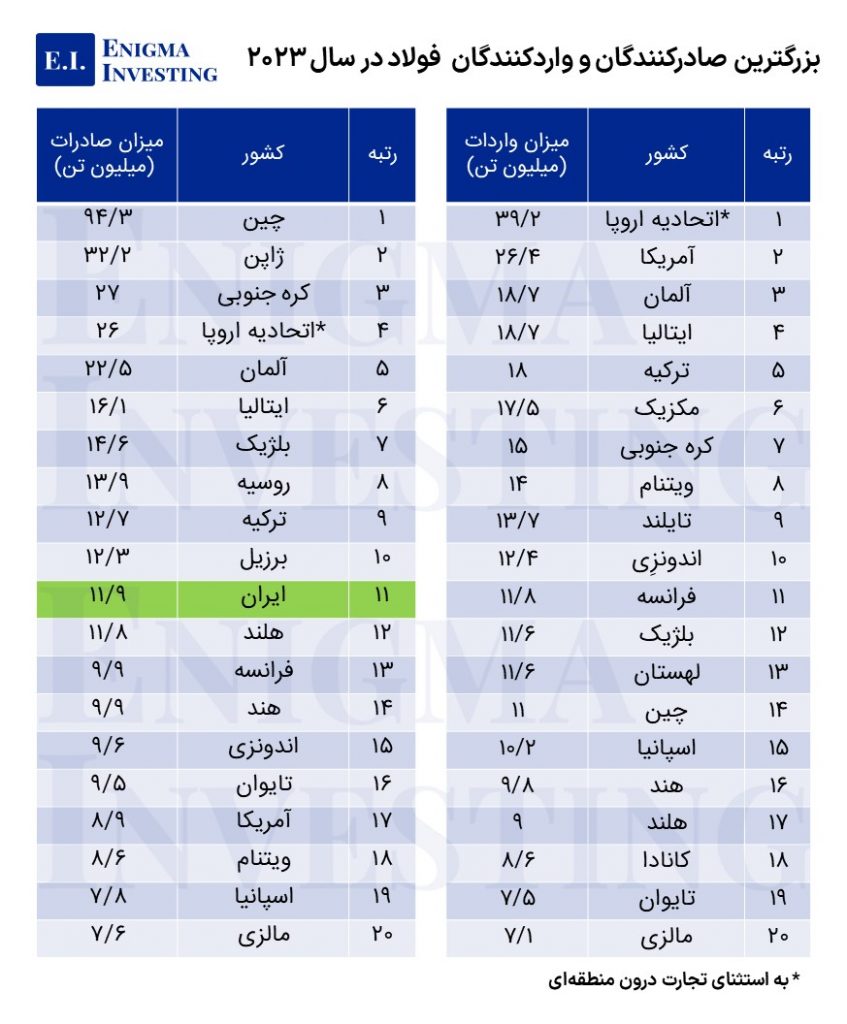
چشم انداز جهانی فولاد
انجمن جهانی فولاد (سایت Worldsteel) جدیدترین پیشبینی تقاضای فولاد را برای سالهای 2024 و 2025 منتشر کرد. براساس پیشبینی این انجمن، تقاضای فولاد در سال جاری (2024) با رشد 1.7 درصدی به 1793 میلیون تن خواهد رسید. همچنین در سال 2025 میزان تقاضای فولاد احتمالا به 1815 میلیون تن برسد. همچنین رییس کمیته اقتصاد جهانی فولاد، درباره چشمانداز این کالا اعلام کرد که به دلیل تداوم سیاستهای انقباضی پولی در دنیا که با رشد هزینههای تامین مالی همراه است و عاملی کاهنده برای ساختوساز به حساب میآید و همچنین عدم قطعیتهای ژئوپلیتیکی احتمالا ضعف در رشد تقاضای جهانی فولاد و نوسانات بالای این بازار را به همراه داشته باشد.
او در ادامه گفته که براساس انتظارات، تقاضای فولاد در چین (به عنوان اصلیترین بازیگر صنعت فولاد) در سال 2024 احتمالا در سطوح سال 2023 باشد، در این خصوص گرچه سرمایهگذاری در بخش املاک و مستغلات همچنان روند کاهشی داشته و افت تقاضا را به دنبال دارد، اما افزایش سرمایهگذاریهای زیرساختی و بخشهای تولیدی منجر به رشد تقاضا شده و افت بخش املاک و مستغلات را جبران میکند. در سال 2025 اما احتمالا تقاضای فولاد چین افت یک درصدی داشته باشد. به استثنای چین، انتظار میرود که طی سالهای 2024 و 2025 تقاضای فولاد در دنیا با رشد 3.5 درصدی همراه شود. هند نیز بهعنوان قویترین محرک رشد تقاضای فولاد از سال 2021 بوده است و پیشبینیها نشان میدهد که تقاضای فولاد هند با رشد 8 درصدی در سالهای 2024 و 2025، همراه شود. علت این امر هم رشد قوی در سرمایهگذاریهای زیرساختی این کشور است.
نکتهای که باید به آن توجه شود، آن است که هزینههای بالای ساختوساز و کمبود نیروی کار محدودیتهایی را برای بسیاری از اقتصادهای بزرگ ایجاد میکند که این موضوع ممکن است رشد بیشتر در زیرساختهای عمومی در برابر افزایش خطرات تغییرات آب و هوایی و سرمایهگذاریهای تاسیسات تولیدی را در کوتاهمدت محدود کند. از سوی دیگر، کاهش سریعتر از حد انتظار تورم همراه با احتمال محدود شدن سیاستهای انقباضی میتواند رونق قابلتوجهی برای بخشهای مصرفکننده فولاد، بهویژه ساختوساز مسکن ایجاد کند. همچنین تسریع در تلاش برای کربنزدایی جهانی یا تلاشها برای تقویت زیرساختهای عمومی در برابر افزایش خطرات تغییرات آب و هوایی، نکات مثبتی هستند که میتوانند از تقاضای جهانی فولاد در آینده حمایت کنند.
در مقابل، احتمال تشدید تنشهای ژئوپلیتیک، فشارهای تورمی پایدارتر از حد انتظار و افزایش سطح بدهی عمومی در اقتصادهای بزرگ ریسکهای مهمی هستند که چشمپوشی از آن اجتنابناپذیر است.
بخش سوم: تحلیل جامع صنعت فولاد در ایران
به رغم آنکه فولاد از دیرباز تاکنون در ایران کاربرد فراوان داشته، اما پیدایش صنعت فولاد در ایران به پیش از جنگ جهانی دوم باز میگردد. در آن سال به دلیل نیازهای کشور به فولاد، قرار بر این بود که پروژه فولادسازی با همکاری با آلمانیها، راهاندازی شود، اما با جنگ جهانی دوم این پروژه ناتمام ماند. آمارها نشان میدهد که اولین کارخانه تولید محصولات فولادی بهنام شرکت ملی ذوب آهن ایران در سال ۱۳۳۸ پایهگذاری شد. امروزه شرکتهای بسیاری در زنجیره فولاد کشور فعالیت دارند. ایران در سال 2023 با تولید31 میلیون تن فولاد، رتبه دهم دنیا را به خود اختصاص داده است. این کشور بزرگترین تولیدکننده فولاد خاورمیانه است.
ظرفیت و میزان تولید و مصرف در صنعت فولاد ایران
در تحلیل جامع صنعت فولاد باید گفت که میزان ظرفیت اسمی فولاد میانی در حال حاضر در ایران برابر با ۴۴ میلیون تن در سال است. طی 11 سال اخیر این کشور به طور میانگین حدود 70 درصد از ظرفیت اسمی خود را تولید کرده که در سال 1402 این عدد به 72 درصد رسیده است. همچنین براساس آمارهای سایت Wordsteel در سال 2023 میزان مصرف فولاد خام ایران 2023 برابر با 19.5 میلیون تن بوده که سرانه مصرف هر ایرانی در کشور بیش از 219 کیلوگرم به ازای هر فرد محاسبه شده است.
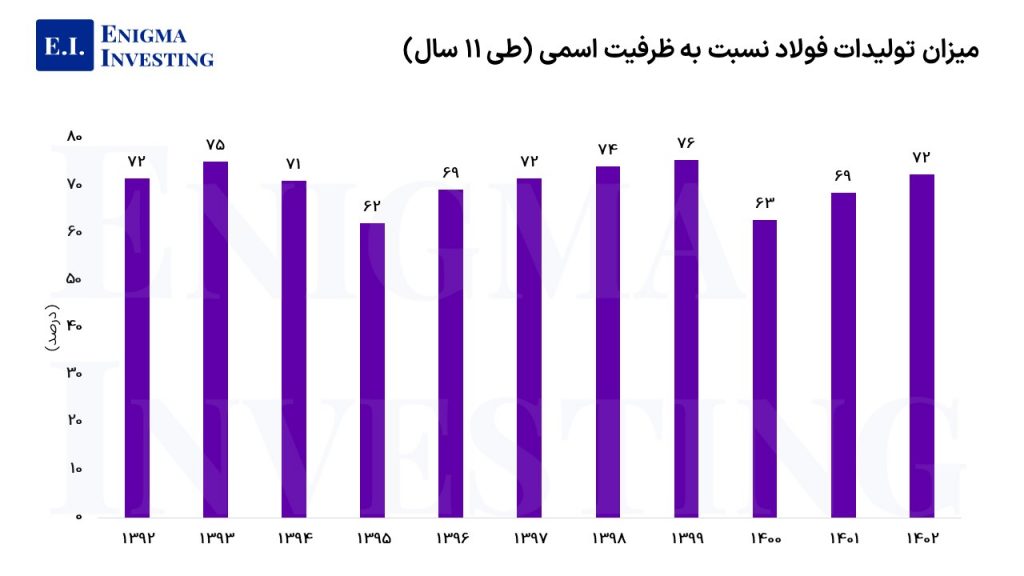
براساس آمارهای انجمن تولیدکنندگان فولاد، در صنایع بالادستی فولاد در سال 1402، 56.7 میلیون تن گندله از سنگ آهن تولید شده که میزان تولیدات این محصول نسبت به سال 1401 با رشد 4.1 درصدی همراه بود. میزان مصرف گندله در این سال برابر با 46.2 میلیون تن بوده است. همچنین در سال گذشته، در فرآیند احیا، 33.4 میلیون تن آهن اسفنجی تولید شد که تولید این محصول نیز نسبت به سال قبلتر 5.2 درصد افزایش داشت.
در 4 ماهه نخست سال 1403، میزان تولیدات گندله 23.3 میلیون تن محاسبه شده که نسبت به دوره مشابه سال قبل رشد 2.1 درصدی دارد. میزان تولیدات آهن اسفنجی نیز در این دوره 14.4 میلیون تن بوده که افزایش حدود 12 درصدی را ثبت کرده است. از جهت مصرف نیز از 33 میلیون تن آهن اسفنجی حدود 32 میلیون تن میزان مصرف این محصول بوده است.
در سال ۱۴۰۲ این کشور حدود ۳۲ میلیون تن فولاد میانی تولید کرده که نسبت به سال 1401 با رشد 5.5 درصدی همراه بود. در واقع طی چند سال اخیر به دلیل مشکلات تامین انرژی و مواد اولیه تولید کشور کاهش یافته بود که در سال 1402 وضعیت اندکی بهبود یافت. در 4 ماهه نخست سال 1403 نیز 10.8 میلیون تن فولاد میانی تولید شده که نسبت به دوره مشابه سال قبل با افت 5 درصدی همراه بوده است.
تصویر ذیل جزییات تولید فولاد میانی طی 4 سال اخیر را نشان میدهد:
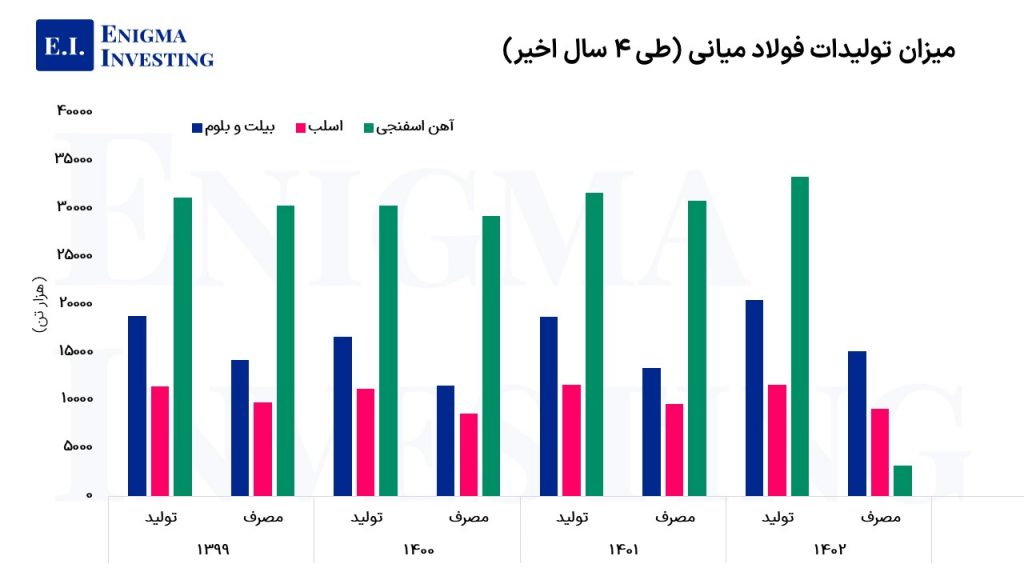
از جهت میزان تولید محصولات نهایی فولادی، در مجموع در سال 1402 حدود 21.5 میلیون تن محصول تولید شده که حدود 58 درصد آن به محصولات مقاطع طویل همچون میلگرد، تیرآهن و… اختصاص دارد. 82 درصد از محصولات طویل مربوط به تولید میلگرد بوده است. از طرفی 42 درصد از کل محصولات نهایی فولاد نیز به مقاطع تخت همچون انواع ورق گرم و سرد اختصاص داشت. به رغم افزایش حدود 5 درصدی مصرف محصولات مقاطع تخت در سال 1402، اما تولید آن کمتر از 0.5 درصد از سال 1401 بیشتر بود.
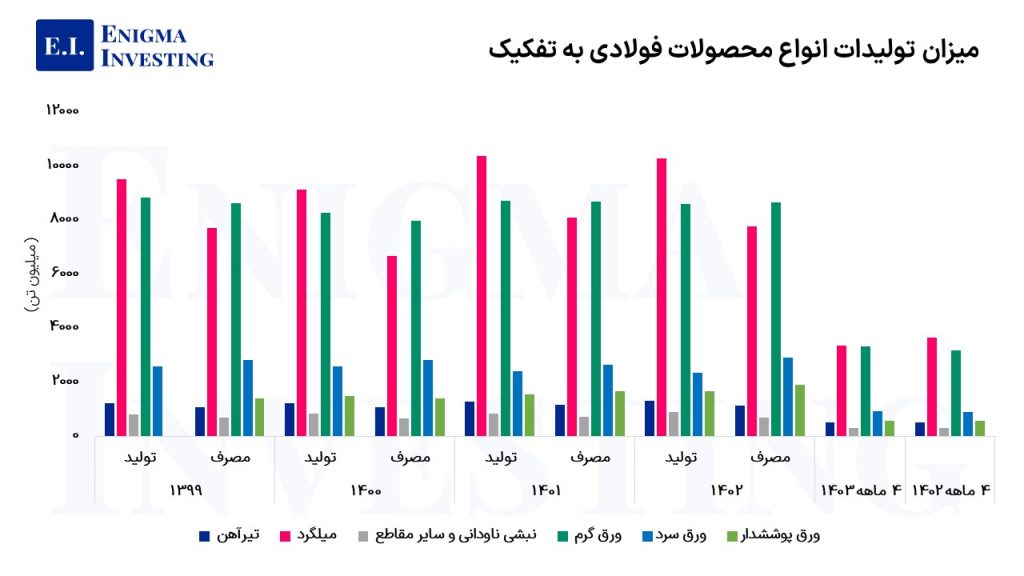
در 4 ماهه نخست سال 1403 نیز در مجموع 7.6 میلیون تن محصولات فولادی تولید شد که 54 درصد آن به مقاطع فولادی طویل اختصاص داشت. در مقاطع طویل میلگرد با سهم 80 درصدی، افت 8 درصدی نسبت به دوره مذکور سال 1402 داشت. سایر محصولات طویل نیز با افت تولید همراه بودند. در محصولات تخت که شامل انواع ورق گرم و سرد بود اما میزان تولیدات کشور در 4 ماهه نخست سال نسبت به دوره مشابه سال 1402 افزایش داشت.
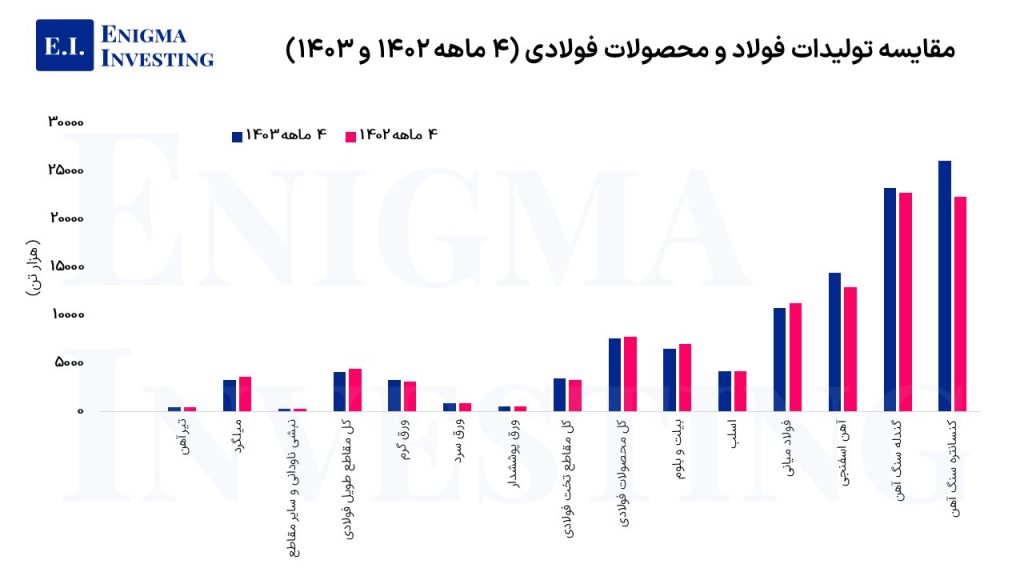
تجارت در صنعت فولاد در ایران
براساس آمارهای Wordsteel ایران در سال 2023 با حدود 12 میلیون تن صادرات به عنوان یازدهمین صادرکننده بزرگ دنیا شناخته شده است. به طور کلی بیشترین صادرات ایران به فولاد میانی همچون اسلب، بلوم و بیلت و همچنین مقاطع طویل فولادی همچون میلگرد و تیرآهن اختصاص دارد. از جهت واردات اما مقاطع تخت فولادی همچون انواع ورق از جمله ورق سرد بیشترین سهم را دارند. در سال 1402 در کل 7.8 میلیون تن فولاد میانی صادر شد. سهم بیلت و بلوم 68 درصد و اسلب 32 درصد از صادرات محصولات میانی فولادی بوده است. همچنین میزان صادرات مقاطع طویل فولادی حدود 7.8 میلیون تن محصول بود که از این میزان 86 درصد به میلگرد اختصاص داشت.
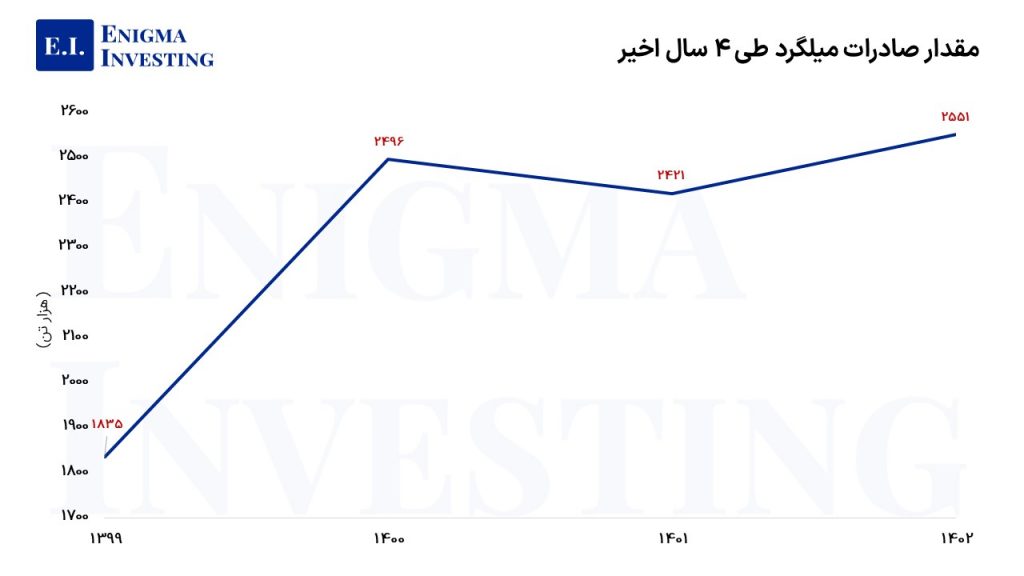
میزان صادرات مقاطع تخت فولادی نیز 482 هزار تن بوده که 86 درصد آن مربوط به ورق گرم بوده است.
در تصویر ذیل روند صادرات فولاد و محصولات فولادی طی 4 سال اخیر آورده شده است:
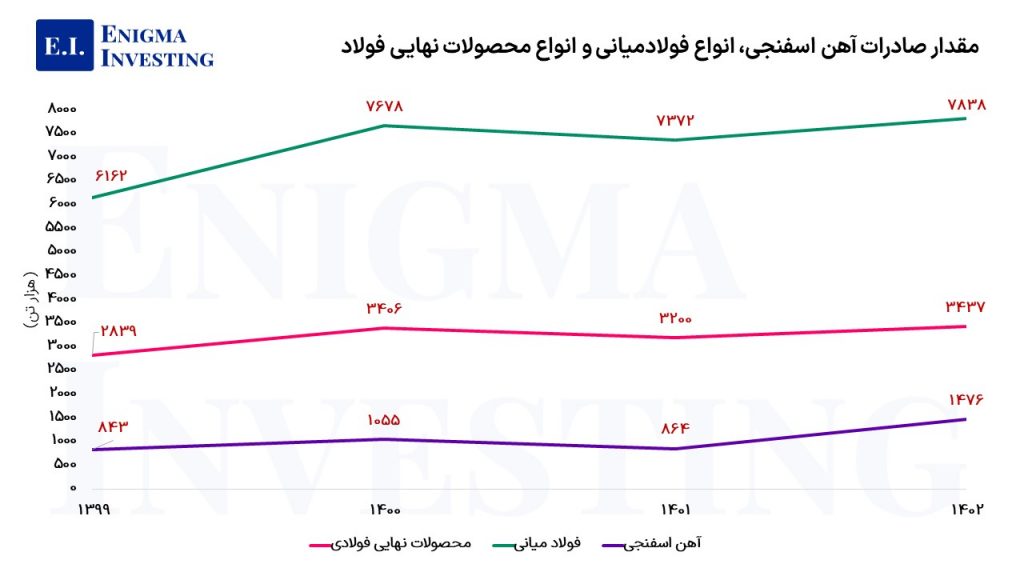
از جهت واردات اما همانطور که گفته شد، بیشترین واردات به انواع ورق به ویژه ورق سرد اختصاص داشته است. در مقاطع طویل انواع نبشی، ناودانی و… نیز سهم نسبتا زیادی از واردات دارند. به طور کلی میزان واردات فولاد میانی حدود 4 هزار تن محصول بوده است. از جهت محصولات نهایی مقاطع طویل حدود 97 هزار تن واردات داشتهاند، این درحالی است که مقاطع تخت حدود 1.4 میلیون تن واردات داشتند که سهم ورق سرد 41 درصد، ورق گرم 35 درصد و ورق پوششدار 20 درصد از واردات محصولات مقاطع تخت بوده است.
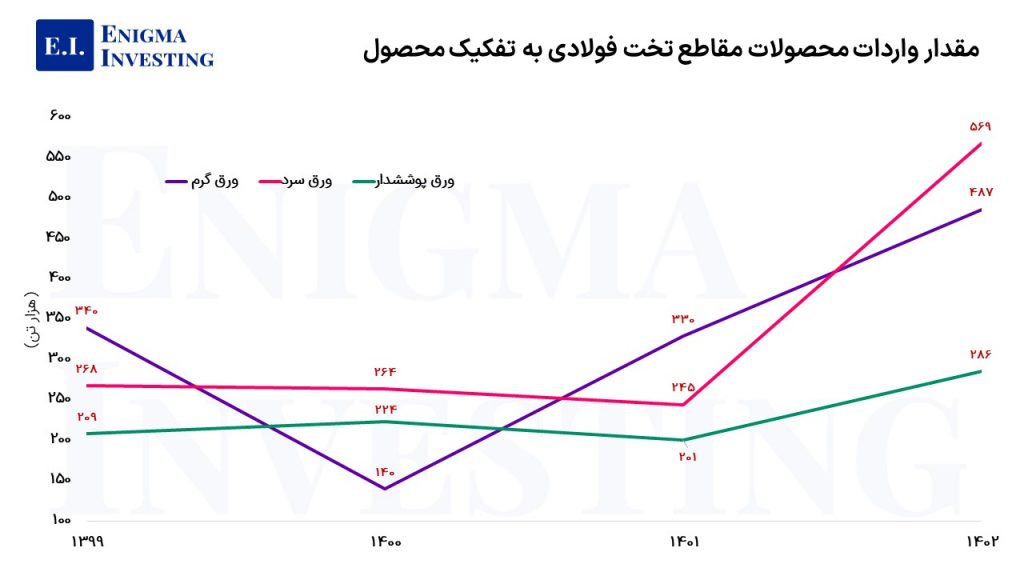
نحوه قیمتگذاری در صنعت فولاد ایران
تا پیش از سال ۱۳۸۲، نرخگذاری در صنعت فولاد براساس قیمتهای تکلیفی دولت تعیین میشد. پس از آن قیمتگذاریها برای مدتی در سازمان كارگزاران بورس فلزات تهران براساس عرضه و تقاضا تعیین شد. با ورود فولاد به بورس کالا، نحوه قیمتگذاری شفافیت بیشتری پیدا کرد. امروزه تمامی تولیدکنندگان زنجیره فولاد موظفند عمده محصولات خود را از طریق بورس کالا به فروش برسانند. معاملات محصولات فولادی در بورس کالا بر مبنای ضرایب قیمتی از نرخ شمش فولاد خوزستان تعیین میشود. نرخ شمش فولاد خوزستان نیز براساس قیمتهای بیلت صادراتی CIS و براساس نرخ دلار نیمایی مشخص میشود.
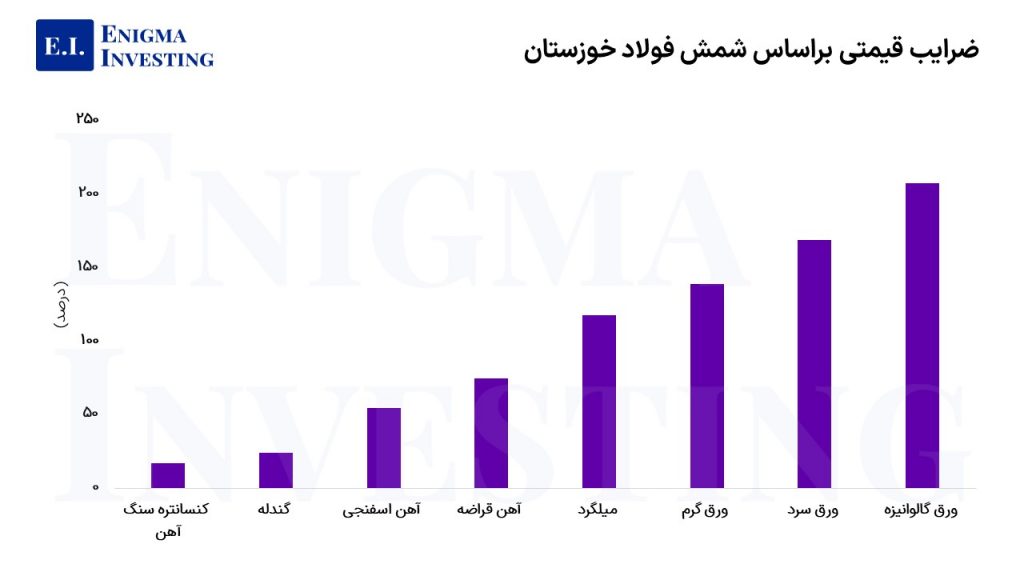
چالشهای صنعت فولاد
تولیدکنندگان زنجیره فولاد با برخی چالشها و مشکلات مواجه هستند که در ادامه اهم آن تشریح شده است:
- مشکلات در حملونقل به ویژه حملونقل ریلی و دریایی
- چالش تأمین انرژی (آب، برق و گاز)
- تعیین عوارض و محدودیتهای صادراتی
- تکنولوژی روز و نوسازی خطوط تولید
- مشکلات اکتشاف و تامین مواد اولیه (سنگ آهن)
- سیاستهای دولت در کنترل غیرمنطقی قیمتها
- بازارهای رقیب در صادرات همچون روسیه و ترکیه
- سیاست تثبیت نرخ ارز و کنترل نرخ دلار توسط دولت
عوامل موثر بر عرضه و تقاضا در صنعت فولادی
در تحلیل بنیادی صنعت فولاد، عوامل موثر بر صنعت فولاد از دو دیدگاه عرضه و تقاضا مورد بررسی قرار میگیرد. این عوامل به تفکیک عرضه و تقاضا در ذیل آورده شده است:
عوامل موثر بر عرضه فولاد در ایران
قیمتهای جهانی: قیمت فولاد در کشور براساس قیمتهای جهانی CIS تعیین میشود. بنابراین هرگونه تغییر در نرخهای جهانی بر نرخهای داخلی نیز اثرگذار است. با توجه به اینکه در ایران صنعت فولاد نقش مهمی در ارزآوری و صادرات دارد، در نتیجه رشد قیمتها منجر به افزایش درآمد شرکتها خواهد شد.
نرخ ارز: با توجه به اینکه بخش مهمی از درآمد فولادیها از صادرات تامین میشود، در نتیجه تغییرات نرخ ارز اهمیت بالایی دارد. نرخ ارز شرکتهای صادراتی بر پایه نرخ نیمایی است. بنابراین افزایش این نرخ رشد درآمد شرکتها را به دنبال دارد و موجب ترغیب بیشتر شرکتها به تولید و صادرات محصولات میشود.
مواد اولیه: سنگآهن به عنوان اصلیترین ماده اولیه در تولید فولاد است. به رغم منابع غنی ایران از سنگآهن اما یکی از مشکلات صنعت فولاد، عقبماندگی در حوزه اکتشاف و مشکلات بهرهبرداری از معادن است. این امر تامین مواد اولیه را با چالش همراه کرده است. بنابراین هرگونه پیشرفت یا پسرفت در حوزه اکتشاف بر صنعت فولاد اثرگذار است.
انرژی: صنعت فولاد یکی از صنایع انرژیبر است که بسته به اینکه شرکتی در کدام بخش زنجیره فولاد قرار دارد، میزان مصرف انرژی آن متفاوت است. انرژی مصرفی زنجیره فولاد شامل گاز، برق و آب است. از جهت میزان گاز مصرفی در بخش احیا بیشترین مصرف وجود دارد. این بخش سالانه حدود 9 میلیارد مترمکعب گاز مصرف میکند. از جهت انرژی برق نیز بیشترین مصرف در قسمت تولید فولاد خام است. این قسمت سالانه 17.35 میلیارد کیلووات برق مصرف میکند. بنابراین هرگونه تغییر قیمت، محدودیت در مصرف و… اثر بسزایی بر هزینههای تولید خواهد داشت. تامین آب نیز یکی از عواملی است که برصنعت فولاد اثر دارد.
سیاستهای دولت: در برخی مواقع قوانین و مقرراتی که دولت برای صنایع مختلف وضع میکند، نقش کاهنده در عرضه را خواهد داشت. برای مثال وضع عوارض صادراتی و تغییرات نرخها بر این صنعت اثرگذار است.
در ذیل میزان عوارض صادراتی زنجیره فولاد آورده شده است:
- سنگ آهن مگنتیت: 20 درصد
- سنگ آهن هماتیت: 2 درصد
- کنسانتره سنگ آهن: 5 درصد
- گندله سنگ آهن: 2 درصد
- آهن اسفنجی: 5 درصد
- بیلت، بلوم و اسلب فولادی: 1 درصد
عوامل موثر بر تقاضای فولاد در ایران
رشد اقتصادی: افزایش تقاضا برای رشد و توسعه زیرساختها، منجر به رشد اقتصادی میشود. از طرفی رشد و توسعه زیرساختها نیاز به تامین مصالح اساسی از جمله فولاد را افزایش میدهد. بنابراین رشد اقتصادی کشور اثر بسیاری برای تقاضای فولاد دارد.
افزایش نرخ ساختوساز: همانطور که گفته شد، بیشترین کاربرد فولاد در ساختوساز است. عمده ساختوساز نیز مربوط به زیرساختهای کشور همچون احداث تونل، پلها و … است. از طرفی رشد ساختوساز مسکن نیز سهم قابل توجهی در میزان مصرف فولاد دارد. بنابراین هرگونه افزایش در پروژههای عمرانی و پروانههای ساختوساز مسکن، منجر به افزایش تقاضای داخلی برای محصولات نهایی فولادی همچون میلگرد و… خواهد شد.
بخش چهارم: تحلیل بنیادی صنعت فولاد در بورس
صنعت فولاد به عنوان یکی از زیرمجموعههای صنعت فلزات اساسی، نیمی از ارزش بازار این صنعت را به خود اختصاص داده است. بزرگترین فولادسازان بورسی شرکتهایی همچون فولاد مبارکه اصفهان، فولاد خوزستان و ذوب آهن اصفهان هستند. بسیاری از افراد، از ذوب آهن اصفهان به عنوان مادر صنعت فولاد ایران، از فولاد مبارکه به عنوان بزرگترین تولیدکننده ورقهای فولادی و از فولاد خوزستان به عنوان بزرگترین تولیدکننده شمش فولادی یاد میکنند.
در حال حاضر میانگین حاشیه سود ناخالص شرکتهای فولادی حدود 25 درصد است که در میان فولادسازان بزرگ، فولاد مبارکه اصفهان حاشیه سود 42 درصدی دارد.
در این خصوص تحلیل بنیادی فولاد را بخوانید.
شرکتهای فولادی در سال 1403 چقدر سود میسازند؟
براساس برآوردهای سایت تحلیلی انیگما میزان سودآوری شرکتهای فولادی در سال 1403 برای تعدادی از فولادسازان بزرگ بورس و فرابورس پیشبینی شده است که در قالب جدول ذیل ارائه شده است:
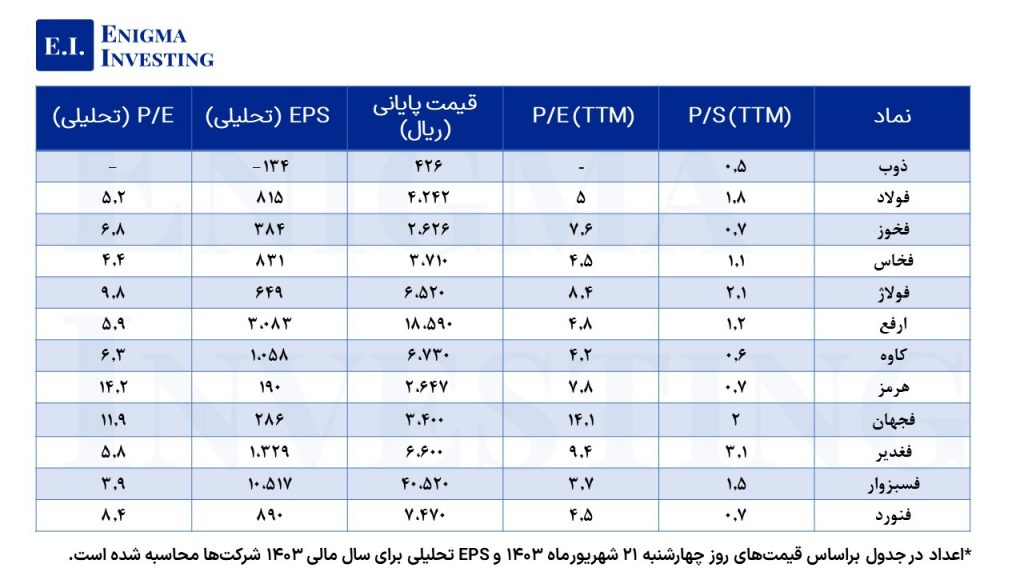